One of the most critical aspects of sheet metal work is creating strong and durable sheet metal joints. A joint is an area where two pieces of sheet metal come together, and it must be carefully designed and constructed to withstand the forces that will be placed on it. There are several different types of sheet metal joints that are commonly used in construction, each with its own strengths and weaknesses.
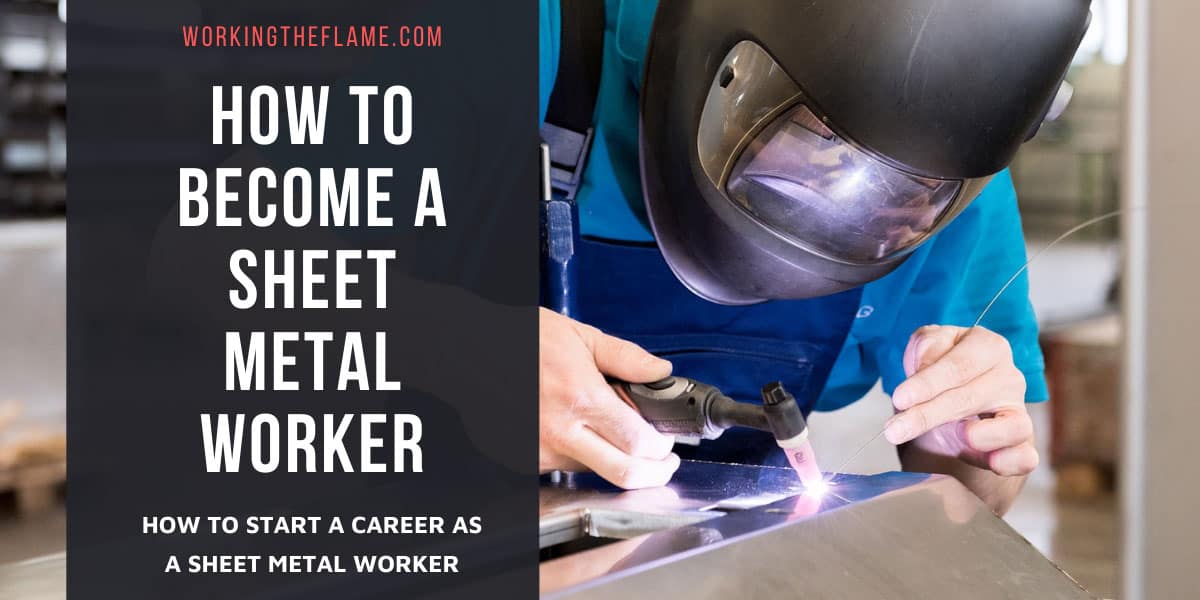
One of the most straightforward sheet metal joints is the butt joint, where two pieces of sheet metal are simply placed end-to-end and welded or soldered together. This type of joint is relatively weak and should only be used in low-stress applications where there is little chance of the joint separating.
Another common type of joint is the lap joint, where one piece of sheet metal is placed over the other and welded or soldered to create a strong bond. Lap joints can be designed with different overlap configurations, and the amount of overlap can be adjusted to increase the joint's strength.
A more sophisticated joint is the T-joint, which consists of two pieces of sheet metal that are welded or soldered together at a right angle. T-joints are stronger than butt joints and are commonly used in structural applications where strength is critical.
Finally, the corner joint is a common joint used in sheet metal work, especially for constructing boxes and other three-dimensional objects. Corner joints can be designed in several different ways, including mitered corners, which are cut at a 45-degree angle, or overlapped corners, which are welded or soldered together at the joint.
In addition to understanding the different types of sheet metal joints, a sheet metal worker must also be skilled in reading engineering and architectural drawings and plans. These documents provide critical information about the intended use of the sheet metal product, the materials that will be used, and the specific measurements and tolerances that must be met.
Overall, sheet metal work requires a combination of technical skill, creativity, and attention to detail. Sheet metal workers must be able to think critically about the best way to design and construct sheet metal products, and they must be able to work efficiently and safely with a wide range of tools and materials. If you're interested in a career in sheet metal work, be prepared to work hard and gain the necessary skills through apprenticeships or formal training programs.